Reducing Delivery Costs: Smart Storage Strategies for GCC Businesses
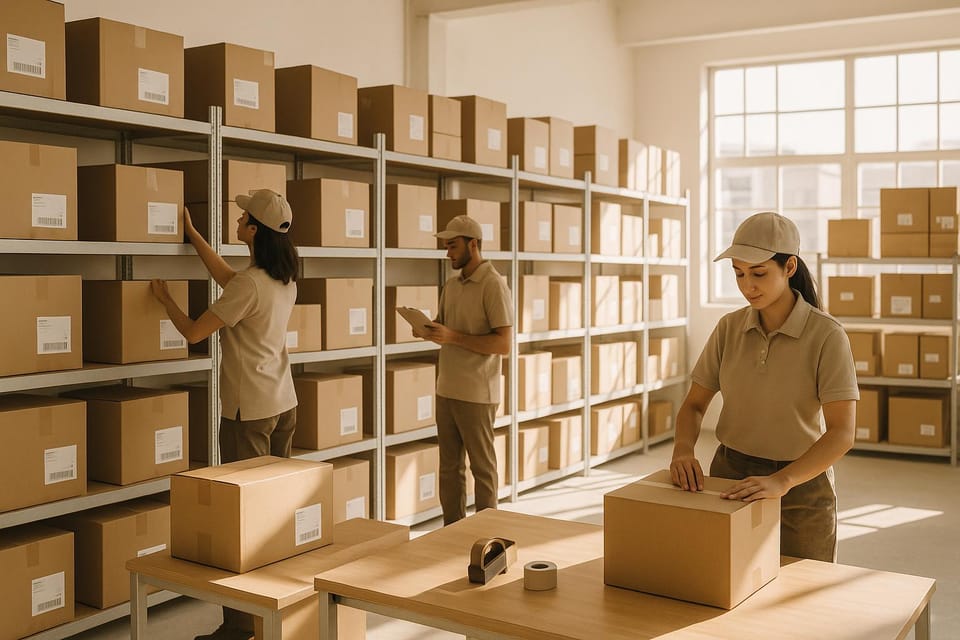
Cutting delivery costs is crucial for businesses in Bahrain and the GCC, where logistics expenses are rising. Here’s how smarter storage strategies can help:
- Vertical Storage Solutions: Use systems like ASRS or VLM to save up to 85% of floor space and reduce labour costs.
- Optimized Warehouse Layouts: Choose layouts (U, I, or L-shaped) to improve picking speed by 30% or more.
- Temperature Control: Maintain ideal conditions to avoid product damage, especially in Bahrain’s humid climate.
- Inventory Management: Implement FIFO and data-driven stock planning to reduce waste and improve efficiency.
- Security Measures: Protect inventory with surveillance, access controls, and insurance options.
Quick Takeaway
By combining these strategies, businesses can lower delivery costs, improve efficiency, and prepare for future growth in Bahrain’s competitive logistics market.
Storage Layout for Better Delivery
Designing an efficient warehouse layout is crucial for boosting delivery speed and cutting costs in Bahrain's competitive logistics industry. Smart storage solutions not only make operations smoother but also help maximise space usage. These improvements naturally lead to the importance of precise storage controls, which will be explored in later sections.
Using Vertical Space Effectively
In Bahrain, where space is often limited, making the most of vertical storage is a game-changer. Systems like Automated Storage and Retrieval Systems (ASRS) can reclaim up to 85% of warehouse space. By optimising space, businesses can also significantly reduce labour and operational expenses.
Another effective solution is Vertical Lift Modules (VLMs), which can boost storage capacity by 40% while also cutting down on picking errors thanks to automation.
For example, Flight Safety achieved impressive results by adopting vertical storage solutions:
- 86% reduction in stockroom labour needs
- 99.9% improvement in picking accuracy
- 85% less floor space required
These results highlight how vertical systems can transform warehouse operations.
Warehouse Layout Planning
A well-thought-out warehouse layout can greatly improve picking speed and streamline delivery processes. Choosing the right design depends on your operational needs and Bahrain's unique climate conditions.
Layout Type | Best Suited For | Key Benefits |
---|---|---|
U-shaped | High-volume operations | Smooth flow for receiving and shipping |
I-shaped | Linear processes | Simplifies inventory movement |
L-shaped | Mixed storage needs | Flexible use of space |
Real-world examples show how impactful the right layout can be:
- CIRRO Fulfillment improved workforce efficiency by 30%, handling 21,000 items daily with robotics.
- JD Logistics maintained 100% picking accuracy while managing over 100,000 SKUs using Automated Case-handling Robots (ACR) systems.
Additionally, modular systems, discussed below, provide even greater flexibility for space optimisation.
Multi-Use Storage Systems
Versatile storage systems not only simplify operations but also help reduce costs. Industrial-grade modular solutions are especially useful for adapting to shifting demands in challenging environments.
For heavy-duty storage needs, Treston offers solutions like:
- Shelving units that can adjust to different product sizes
- ESD protection for sensitive electronics
- Modular designs that expand alongside business growth
As Chris Lebel, owner of Industrial Automation Supply, puts it:
"Modula is a great product, and it has been key in our future growth. We can do much more, much better with much less."
Innomed's experience further underscores this point:
"If we wanted to stay in our current building, we had to utilise vertical space for extra storage. The Modula system was able to store approximately 90% of our inventory – we couldn't believe it!"
These examples show how adaptable storage systems can meet diverse needs while supporting business growth.
Temperature Control for Storage Success
Managing temperature and humidity effectively in Bahrain is crucial for reducing product damage and keeping delivery costs in check.
Temperature and Humidity Guidelines
Maintaining stable conditions is key to avoiding costly damage.
Storage Type | Temperature Range | Humidity Range | Notes |
---|---|---|---|
General Goods | 13°C to 20°C | 35% to 60% RH | Best for items like paper, leather, and wood |
Electronics | 18°C to 22°C | Below 30% RH | Protects against corrosion |
Sensitive Materials | 15°C to 18°C | 45% to 50% RH | Requires close monitoring |
Humidity levels above 90% RH can accelerate corrosion rates by up to six times compared to environments kept below 50% RH. This is especially important during Bahrain's summer months when humidity often soars past 90% RH. These temperature and humidity standards align with earlier storage layout strategies, ensuring inventory remains protected and in optimal condition.
Protection from Moisture Damage
Given Bahrain’s humid climate, controlling moisture is a top priority. Dehumidifiers can reduce energy usage by up to 60% compared to direct heating solutions. To safeguard goods effectively:
- Install durable dehumidifiers: Use non-corrosive materials to withstand the coastal air's high salt levels.
- Choose moisture-resistant materials: Opt for containers and packing materials designed to resist humidity.
- Elevate storage: Keep items off the ground to avoid contact with moisture.
- Use moisture absorbers: Place these strategically throughout storage areas.
"Excess warehouse humidity can lead to mold, product damage, and equipment corrosion, making a high-performance industrial dehumidifier for warehouses essential for maintaining optimal conditions." - Ctrltech
Air Flow Management
In addition to controlling moisture, proper ventilation is critical for maintaining stable conditions. When humidity surpasses 70% RH, it creates the perfect environment for mold growth.
To ensure effective air circulation:
- Use fans, maintain proper spacing between items, and rely on sensor-driven systems to prevent humidity buildup .
- Install temperature sensors at the warmest and coolest points in the warehouse, identified through seasonal mapping.
- Monitor humidity at central points in each storage zone, as it tends to spread quickly across spaces.
Inventory Management Methods
Managing inventory effectively plays a key role in cutting delivery costs by reducing waste and improving storage efficiency. Using well-established methods not only lowers operational expenses but also ensures product quality remains intact.
Product Placement by Demand
Strategic product placement can significantly cut down on picking times - up to 40% - by ensuring that frequently accessed items are stored in the most convenient locations. This approach reduces handling time and movement costs.
Zone Type | Placement Location | Benefits |
---|---|---|
Fast-Moving Items | Near docks or shipping areas | Saves travel time |
High-Value Products | Golden zone (waist-height) | Speeds up picking by 40% |
Seasonal Goods | Flexible storage areas | Maximizes adaptability of storage use |
Slow-Moving Items | Upper shelves or back areas | Keeps prime locations available |
Once product placement is optimized, managing perishable goods becomes a priority, especially with the use of FIFO techniques.
FIFO for Fresh Goods
The First-In, First-Out (FIFO) method is essential for handling perishable inventory. For example, Esnelat, a dairy business, manages 350,000 pallets annually while ensuring traceability at every step.
Key steps for implementing FIFO include:
- Labelling zones clearly with production dates and batch numbers.
- Using warehouse management systems for real-time inventory tracking.
- Conducting regular inventory audits to avoid spoilage and obsolescence.
"The software is capable of optimising movement, ensuring traceability and speed in the execution of tasks. In addition, it allows us to efficiently receive all goods coming from different work centres, knowing in advance all the information on the products pending arrival."
Data-Driven Stock Planning
Going beyond placement and rotation, integrating real-time data into stock planning enhances inventory management further. AI-powered, cloud-based systems provide insights to predict demand and maintain optimal stock levels.
"Consumer behaviour has changed radically in recent years, leading to the transformation of the retail landscape and the growth of online shopping... Appropriate warehouse infrastructure will be required to meet rising customers' expectations."
These methods, when combined, contribute to reducing delivery costs and improving operational efficiency, aligning with Bahrain's growing logistical demands.
Storage Security Measures
Bahrain's warehouses are equipped with advanced security systems to protect inventory, minimise theft, and control costs effectively.
Package Security and Monitoring
Modern surveillance systems play a key role in safeguarding stored goods. The GCC video surveillance camera market is expected to reach around BHD 1.50 billion by 2033. Key tools enhancing security include:
- High-resolution IP cameras for clear, detailed footage
- AI-powered threat detection to identify potential risks automatically
- Smart environmental sensors to monitor conditions like temperature and humidity
- Digital tracking systems to keep tabs on inventory movement
"We are now hyper-focused on delivering practical functionalities that address real-world needs. The Middle East and North Africa, with its diverse security needs, is the perfect stage to showcase our industry-leading AI-powered surveillance solutions."
- Nam Sik Yoon, Managing Director, Hanwha Vision MEA FZE
These tools not only improve security but also support better access management within warehouses.
Warehouse Entry Controls
To manage and restrict access, warehouses employ multi-layered security measures such as:
- Biometric access controls to ensure only authorised personnel can enter
- Digital entry/exit logs for accurate tracking of movement
- Secure zones dedicated to sensitive operations
- Emergency response protocols to handle unexpected incidents
An example of these measures in action is Dubai Police's smart security system, introduced at Gitex Global Expo in October 2024. This system uses mobile-integrated sensors to detect movement and send instant alerts.
While physical access is tightly controlled, additional protection through insurance ensures comprehensive risk mitigation.
Storage Insurance Options
Insurance plays a critical role in protecting inventory from theft, damage, and environmental risks. Businesses in Bahrain can choose from several insurance options:
Insurance Type | Coverage Description | Business Impact |
---|---|---|
Property All-Risk | Covers a wide range of potential hazards | Broad protection for assets |
Stock Throughput Policy | Includes goods in transit and storage | Ensures operational continuity |
Warehouse Legal Liability | Protects against damage to stored property | Reduces risk of legal claims |
Fidelity Guarantee | Covers losses from employee fraud | Limits internal financial risks |
"A stock throughput policy (STP) is a marine cargo policy designed for companies that import, distribute, or export merchandise."
- Marsh
Conclusion: Cost Savings Through Better Storage
Main Points Summary
Efficient storage strategies can significantly reduce delivery costs for businesses across the GCC. According to recent data, warehouses operating at peak efficiency reach an average utilization rate of 85.6%, highlighting how smart storage solutions can directly impact operational expenses.
Strategy | Impact | Cost Benefit |
---|---|---|
Vertical Storage Solutions | Maximizes space usage | Cuts the need for additional facilities |
Real-time Inventory Tracking | Enhances inventory management | Reduces excess stock and working capital |
Climate Control Systems | Maintains ideal storage conditions | Protects product quality, reduces energy |
Advanced Security Measures | Safeguards assets and prevents losses | Lowers insurance expenses |
When combined with advanced tools like Warehouse Management Systems (WMS), these strategies further boost efficiency. In fact, the WMS market is expected to reach BHD 1.55 billion by 2025, underscoring its role in streamlining operations and cutting delivery costs.
Planning for Future Growth
While immediate cost reductions are valuable, scalable storage solutions also ensure long-term competitiveness. For example, the logistics hub at Dubai Mall adopted a modular warehouse system that not only increased storage capacity but also reduced energy usage, enabling more efficient delivery operations. This forward-thinking approach not only secures current savings but also prepares businesses for future challenges.
For companies planning to expand, these considerations are essential:
- Space Optimization: Flexible modular systems can address Bahrain's shifting storage needs. Currently, 47% of facilities report space shortages.
- Technology Integration: Using predictive analytics can cut supply chain disruptions by 30%, ensuring smoother and more efficient operations.
- Energy Efficiency: Initiatives like the GCCA Energy Excellence Recognition Programme help temperature-controlled facilities reduce energy waste.
"Cost optimization strategically manages resources to drive growth and sustainability." - InOrg
FAQs
How can vertical storage systems like ASRS and VLM help businesses in Bahrain lower delivery costs?
Vertical storage solutions like Automated Storage and Retrieval Systems (ASRS) and Vertical Lift Modules (VLM) offer businesses in Bahrain an efficient way to cut delivery costs while optimising warehouse operations and space utilisation. These systems allow for more inventory to be stored within a smaller area, reducing rental costs and eliminating the need for costly facility expansions.
By making the most of vertical space, VLMs can free up to 90% of floor space compared to traditional shelving. They also boost picking speed and accuracy, which lowers labour costs and reduces mistakes that could delay shipments. ASRS systems take efficiency a step further by simplifying inventory management, enabling faster and more dependable order processing. Together, these technologies help businesses in Bahrain streamline last-mile logistics and significantly reduce delivery expenses.
How can businesses in Bahrain maintain proper temperature and humidity in warehouses to protect stored goods?
To protect products from Bahrain's hot and humid climate, it's crucial to maintain proper temperature and humidity levels in warehouses. For most items, temperatures should stay within 18°C to 24°C, while frozen goods require storage below -18°C. Keeping relative humidity between 30% and 50% helps prevent moisture-related damage.
Investing in climate control systems like dehumidifiers and temperature monitors can make it easier to maintain these conditions. Using proper insulation and materials that resist humidity is equally important. Good ventilation and consistent airflow are also key to avoiding temperature swings and humidity build-up, ensuring your inventory remains in good condition over time.
How can a FIFO inventory system help GCC businesses reduce costs and improve logistics efficiency?
Implementing a FIFO (First In, First Out) inventory system can make a big difference for businesses in the GCC. This method ensures that older stock is sold or used first, which is especially useful for managing perishable goods. By reducing waste from spoilage or outdated products, businesses can save money and operate more efficiently. Plus, FIFO helps keep inventory organised and visible, making it easier to monitor stock levels and adjust as needed.
From a financial perspective, FIFO helps businesses sell older, often lower-cost items before newer, higher-cost ones. This approach not only improves profit margins but also supports healthier cash flow. In Bahrain, where high temperatures make climate-controlled storage a necessity, FIFO ensures products move quickly, reducing the risk of damage and maintaining quality. This efficiency leads to happier customers and better overall operations.