Inventory Turnover Benchmarks for GCC Businesses
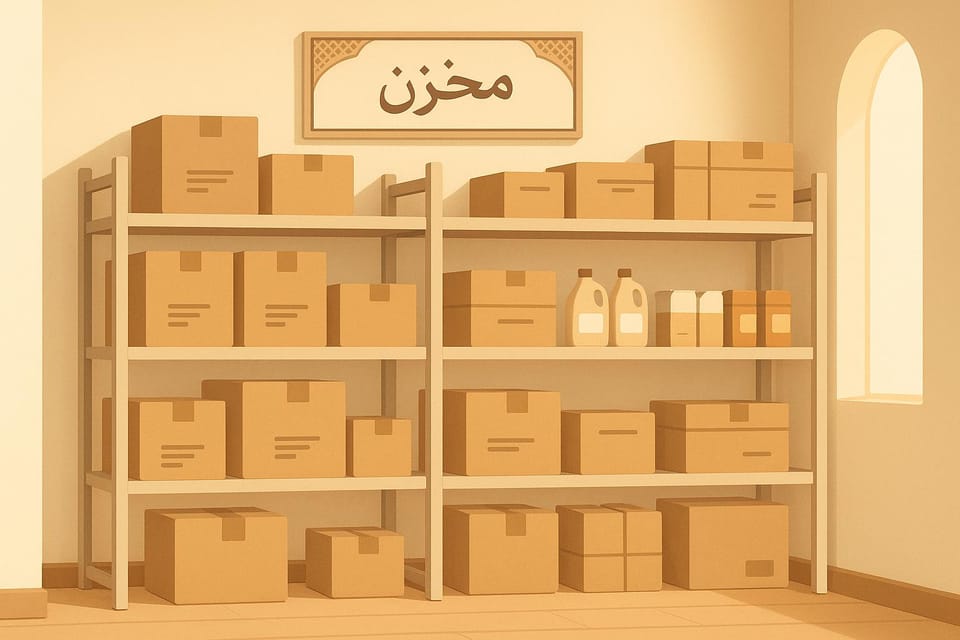
Managing inventory efficiently is critical for businesses in Bahrain and the GCC region to stay competitive and profitable. Here's what you need to know:
-
What is Inventory Turnover? It measures how quickly businesses sell and replace stock. Formula:
Inventory Turnover = Cost of Goods Sold ÷ Average Inventory Value
Example: If a Bahraini retailer has a BHD 500,000 annual cost of goods sold and BHD 100,000 in average inventory, the turnover ratio is 5 (stock replenished five times annually). -
Key GCC Challenges:
- Climate: Hot, humid conditions require temperature-controlled storage, increasing costs.
- Imports: Long lead times due to reliance on imported goods.
- Seasonal Trends: Ramadan and Eid cause demand spikes, requiring flexible inventory strategies.
-
Industry Insights:
- Retail: FMCG has high turnover due to demand; luxury goods have slower rates.
- Food Storage: Climate control is essential to prevent spoilage.
- Construction Materials: Moisture-proof and climate-controlled storage is crucial to protect quality.
-
Tech Solutions in Bahrain:
- Digital Systems: 42% of SMEs use digital inventory tools, with costs ranging from BD 2,000 to BD 15,000. Government grants cover up to 50%.
- RFID Benefits: Improved accuracy (+27%), reduced stockouts (-65%), and better turnover (+31%).
- Cloud and Mobile Tools: Real-time tracking, 60–70% lower costs, and reduced spoilage by 30–35%.
Actionable Tips:
- Use digital inventory systems like RFID for better tracking and efficiency.
- Invest in climate-controlled storage to protect goods.
- Leverage cloud-based tools for real-time updates and automated reordering.
- Monitor key metrics like turnover rates regularly.
Efficient inventory management is essential for thriving in Bahrain's unique market conditions. Start with these strategies to improve your operations today.
Inventory Turnover Ratio Formula & Calculation : Step-by-Step tutorial in Excel
Inventory Turnover Basics
Inventory turnover is a critical metric that helps businesses measure how effectively they manage their stock. It tracks how often inventory is sold and replaced over a specific period. This is particularly important in the fast-paced GCC markets, where efficient stock management plays a key role in maintaining profitability and smooth operations, especially given the region's unique challenges.
Calculating Inventory Turnover
The formula for calculating inventory turnover is straightforward:
Inventory Turnover Ratio = Cost of Goods Sold ÷ Average Inventory Value
Let’s break it down with an example: Imagine a retailer in Bahrain with an annual cost of goods sold amounting to BHD 500,000 and an average inventory value of BHD 100,000. Using the formula, the turnover ratio comes out to 5, meaning the retailer replenishes its stock five times a year.
While a higher turnover ratio often signals efficient inventory management, the ideal ratio depends on the industry. Factors like the type of products sold and the demand in the market play a significant role in determining what’s optimal. This calculation provides a foundation for understanding how specific regional factors in the GCC influence inventory turnover.
GCC Market Factors
In the GCC, inventory turnover is shaped by more than just standard calculations. Several regional factors come into play:
- Import Dependencies: Many goods in the GCC are imported, leading to longer lead times. Businesses often maintain buffer stocks to mitigate delays.
- Climate Challenges: The region's high temperatures require reliable climate control systems, especially for storing perishable goods.
- Seasonal Trends: Events like Ramadan bring noticeable shifts in demand, requiring businesses to adjust inventory levels accordingly.
These regional dynamics make inventory turnover a more nuanced metric in the GCC, requiring businesses to adapt their strategies to stay efficient and competitive.
GCC Industry Turnover Standards
Industries across the GCC display distinct turnover patterns influenced by product characteristics and storage requirements. These patterns are crucial for managing inventory efficiently in a region known for its challenging climate. By combining basic calculations with market dynamics, these benchmarks provide insight into how regional and industry-specific factors shape turnover practices.
Retail Sector Analysis
In the retail industry, turnover rates differ significantly between fast-moving consumer goods (FMCG) and luxury items. FMCG products, such as groceries and household essentials, require frequent restocking due to their high demand and shorter shelf life. On the other hand, luxury goods tend to have slower turnover rates, reflecting their niche appeal and higher price points. Supermarkets in Bahrain often address these needs through advanced storage solutions, including multi-temperature zones that cater to the diverse storage needs of FMCG and other products. This focus on adaptable storage solutions aligns with Bahrain's push for modern inventory management systems.
Food Storage Requirements
Storing food in the GCC comes with unique challenges due to the region's high temperatures. Perishable goods must be kept in temperature-controlled environments to maintain freshness, while non-perishable items offer more flexibility. Key practices for food storage include maintaining steady temperatures, managing humidity levels, and implementing a first-in, first-out (FIFO) system to minimise spoilage and waste. These measures are essential for ensuring food safety and quality in the region's extreme climate.
Construction Materials Management
The management of construction materials in the GCC is heavily influenced by the harsh weather conditions. Turnover rates for these materials vary depending on their type and usage. Basic materials, such as cement and aggregates, require moisture-proof and covered storage to prevent damage. Meanwhile, specialised materials, such as finishing products or equipment, often need climate-controlled environments to maintain their integrity. Proper storage practices are critical to preserving the quality of these materials and ensuring their usability in construction projects across the region.
Weather and Season Effects
The intense heat and humidity typical of the GCC region pose unique challenges for inventory management. Without proper storage solutions, these conditions can quickly damage goods. To safeguard product quality and maintain efficient inventory turnover, businesses must invest in reliable climate-controlled storage systems and adapt their operations to account for temperature fluctuations and seasonal holidays.
Temperature Control Methods
Warehouses in Bahrain rely on sophisticated climate control systems to maintain ideal storage conditions. This includes frequent temperature checks, dehumidifiers to reduce moisture levels, and high-quality insulation to prevent heat buildup and condensation. These measures are crucial for preserving sensitive items and prolonging their shelf life.
Holiday Period Planning
Seasonal events and holidays, such as Ramadan and Eid, significantly impact consumer behaviour and inventory cycles in the GCC. For example, perishable goods may require increased cold storage capacity during these high-demand periods. By anticipating these seasonal shifts, businesses can adjust their storage and inventory strategies to ensure products are well-protected against environmental factors while meeting market demands.
Digital Tools for Inventory Control
The way inventory is managed in the GCC region, including Bahrain, has been reshaped by digital tools. For instance, around 42% of Bahraini SMEs now use digital inventory systems, though only 18% have fully integrated solutions in place.
Bahrain SME Tech Usage
In Bahrain, small and medium enterprises are increasingly adopting digital inventory tools because they deliver clear benefits in cost savings and operational efficiency. The cost of implementing these systems typically ranges between BD 2,000 and BD 15,000, depending on the size of the business and the complexity of the system. To ease this financial burden, government-backed grants can cover up to 50% of these costs. Businesses report several advantages, such as:
- 15–20% cost reductions
- Improved cash flow and better product availability
- 20–25% savings in labour costs related to inventory management
Beyond cost savings, specific technologies like RFID (Radio-Frequency Identification) have shown remarkable results.
RFID Results in Retail
RFID technology has proven to be a game-changer for inventory management, particularly in retail. Here's how it has improved key performance metrics:
Performance Indicator | Pre-RFID | Post-RFID | Improvement |
---|---|---|---|
Inventory Accuracy | 70% | 97% | +27% |
Stockout Reduction | Baseline | -65% | 65% |
Labour Cost Savings | Baseline | -22% | 22% |
Inventory Turnover | Baseline | +31% | 31% |
For example, a well-known Bahraini department store chain achieved a 31% improvement in inventory turnover, outperforming the GCC average of 25%. These advancements are part of a broader ecosystem that includes cloud systems, mobile apps, and analytics tools.
Cloud, Mobile, and Analytics: The Bigger Picture
Cloud-based inventory systems are particularly attractive because they reduce upfront costs by 60–70% and offer real-time visibility into inventory levels. This is especially beneficial for industries handling temperature-sensitive products. IoT sensors combined with automated monitoring systems have helped cut product spoilage by 30–35%, while also reducing manual monitoring costs by 40–45%.
Mobile applications are another key tool, with adoption rates increasing by 45%. These apps help businesses save 35–40% task time, reduce errors by 25–30%, and improve inventory turnover by 18–22%. Meanwhile, advanced analytics tools enhance decision-making by cutting forecast errors by 25–30%, optimizing safety stock by 15–20%, and flagging slow-moving items more effectively.
For businesses looking to refine their inventory management strategies or explore digital tools, local resources like Mukani provide tailored guides and actionable tips specifically for the GCC market.
Summary and Action Steps
Here are some practical ways to improve inventory management:
- Leverage Technology: Invest in digital inventory systems equipped with RFID technology. This not only simplifies tracking but also improves overall efficiency.
- Maintain Climate-Controlled Storage: Keep storage areas at the right temperature and humidity levels to protect your inventory. Proper packing methods can also shield items from dust and other potential damage.
- Use Cloud-Based Systems: Implement cloud-based tracking solutions for real-time updates. Automated reordering can help ensure stock levels are always optimal.
- Track Performance Metrics: Regularly monitor key metrics like stock accuracy and turnover rates to pinpoint areas that need attention.
These approaches align with practices commonly seen in the GCC region, helping to strengthen your inventory management strategy. For more tailored advice, Mukani provides valuable guidance specific to GCC industries.
FAQs
How do GCC climate conditions impact inventory turnover and management strategies?
The climate in the GCC region, including Bahrain, plays a big role in shaping how businesses manage their inventory. With high temperatures, humidity, and the occasional dust storm, certain products - like perishables, electronics, or items sensitive to environmental factors - can deteriorate faster. This makes climate-controlled storage solutions a must for maintaining product quality and minimising losses.
Seasonal demand also adds another layer of complexity. For example, summer cooling appliances and winter clothing see spikes in sales depending on the time of year. To keep up, businesses need to adjust their stock levels to match local buying patterns. On top of that, using proper packing methods, secure storage, and conducting regular inventory checks can help protect goods from damage, theft, or environmental risks while improving overall efficiency.
What benefits does RFID technology offer for inventory management in GCC businesses, and how does it compare to traditional methods?
RFID technology brings a host of advantages to inventory management for businesses in the GCC, positioning it as a modern upgrade over older methods like barcode scanning or manual tracking. Here’s why it stands out:
- Real-time tracking: With RFID, businesses can monitor inventory instantly, cutting down on errors and ensuring greater accuracy.
- Time-saving efficiency: Unlike barcodes, RFID tags can be scanned in bulk without needing a direct line of sight, making stock counts significantly faster.
- Improved security: RFID offers precise tracking of goods, helping to reduce theft and loss.
When compared to traditional methods, RFID proves to be quicker, more dependable, and far better equipped to manage large inventory volumes. While the initial setup might require a higher investment, the long-term gains in efficiency and accuracy make it a smart choice for businesses in Bahrain and throughout the GCC.
How can businesses in the GCC, including Bahrain, manage seasonal demand spikes like those during Ramadan and Eid to improve inventory turnover?
To handle seasonal demand surges during times like Ramadan and Eid, businesses in the GCC need to plan their inventory smartly. Start by digging into past sales data to spot trends and adjust stock levels to match expected demand. It's also a good idea to coordinate with suppliers well in advance to ensure timely deliveries, helping you avoid either running out of stock or ending up with too much.
Using just-in-time inventory methods can be a practical way to reduce excess stock while still meeting customer needs. At the same time, keeping customers informed about promotions and product availability can boost sales during these busy periods. For surplus inventory, consider storing items in climate-controlled spaces to shield them from Bahrain’s intense heat and humidity, ensuring they remain in top condition.