How to Set Up an Efficient Packing Station for E-commerce
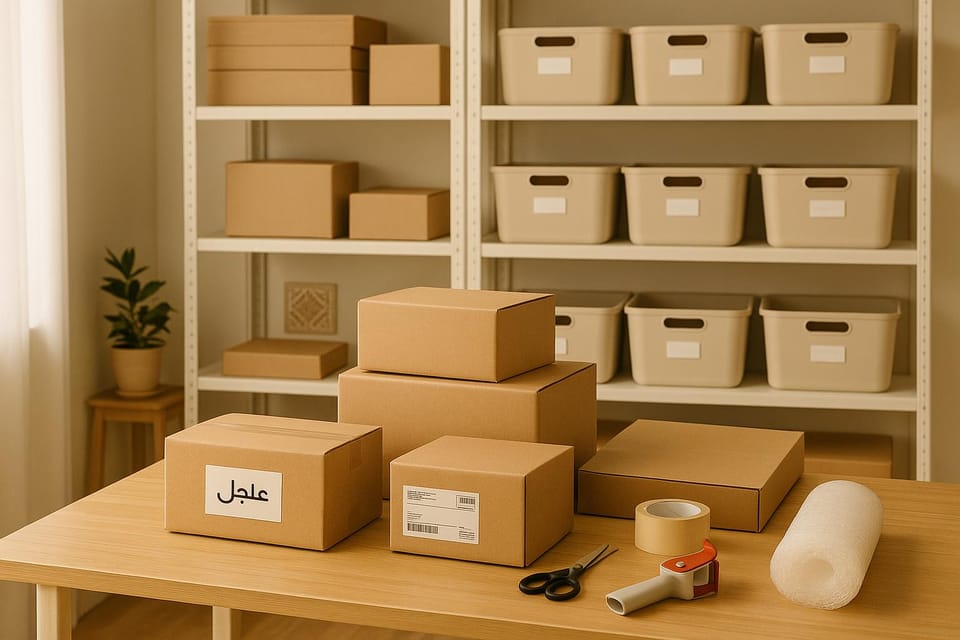
An organized packing station is critical for reducing shipping errors, speeding up order processing, and improving customer satisfaction. In Bahrain’s growing e-commerce market - expected to reach BD 468.2 million by 2025 - efficient packing processes can give your business a competitive edge.
Key Takeaways:
- Cut Costs and Errors: A well-structured setup reduces costly returns caused by shipping mistakes.
- Boost Productivity: Smart layouts like U-shaped designs save space and streamline workflows.
- Handle Bahrain’s Climate: Use climate-smart storage and weather-resistant materials to protect goods from heat and humidity.
- Stay Scalable: Plan for growth by implementing automated systems and ergonomic designs.
Quick Tips for Success:
- Choose the Right Layout: U-shaped workspaces are ideal for small spaces (50–100 m²) and high-volume operations.
- Use Smart Storage: Vertical racks, modular bins, and climate-controlled units keep inventory organized and safe.
- Invest in Tools: Label printers, industrial tape dispensers, and bilingual barcode scanners ensure speed and accuracy.
- Prepare for Heat: Install cooling systems, dehumidifiers, and use heat-resistant packing materials.
- Track Performance: Monitor order accuracy, processing time, and customer satisfaction to improve operations.
Efficient packing stations aren’t just about organization - they’re about building a foundation for long-term growth in Bahrain’s fast-evolving e-commerce market.
3 Tips for Designing Your Own Packing Station Flow
Step 1: Planning Your Packing Station Layout
Setting up an efficient packing station is key to speeding up order processing while ensuring product quality - especially in Bahrain, where high ambient temperatures can pose challenges.
Linear vs. U-shaped Workspaces
When it comes to workspace design, U-shaped layouts are a favourite among Bahrain's e-commerce businesses. They position shipping and receiving docks side-by-side, allowing shared dock resources and smoother product handling.
Layout Type | Space Needed | Best For | Key Benefits |
---|---|---|---|
U-shaped | 50–100 m² | High-volume operations | – Shared dock resources – Efficient cross-docking – Reduced product handling |
Linear (I-shaped) | 100+ m² | Bulk storage needs | – Straight product flow – Larger sorting areas – Better ventilation |
L-shaped | 75–150 m² | Mixed operations | – Flexible storage options – Adjacent dock placement – Balanced workflow |
For smaller operations managing up to 50 orders per day, a U-shaped layout in a 50 m² space is a practical choice. This setup ensures efficient dock usage and simplifies product movement, making it ideal for compact spaces.
Once the workspace is configured, the next step is to optimise storage solutions for a seamless packing process.
Space-saving Storage Solutions
Modern storage systems are designed to save space while maintaining the right conditions for sensitive goods, even during Bahrain's hot summer months.
-
Vertical Storage Systems
These systems make the most of vertical space, reducing the floor area required. Automation levels can vary, so costs will depend on the features you choose. -
Climate-Smart Modular Solutions
Designed to handle extreme heat, these storage units ensure products remain in optimal condition, even during Bahrain's peak summer temperatures. -
Smart Bin Systems
Modular smart bins offer a great way to organise temperature-sensitive items. Pair them with a clear labelling system using alphanumeric codes to keep everything in order. This is particularly useful during high-demand periods like Ramadan and Eid, when order volumes tend to surge.
Step 2: Required Equipment and Local Suppliers
Once your layout is ready, it’s time to set up your station with the right tools and materials to streamline operations and safeguard inventory from Bahrain’s challenging climate.
Basic Packing Tools Checklist
To keep your packing process efficient, ensure you have these essential tools on hand:
Equipment Category | Essential Items |
---|---|
Packing Tools | • Industrial tape dispensers • Label printers (Arabic/English) • Box cutters with safety locks |
Storage Solutions | • Mobile packing carts |
You can source these items from local suppliers. For instance, United Paper Industries' Bahrain Pack, located in Sitra Industrial Park, offers a wide range of packaging supplies and operates the largest corrugated box manufacturing facility in Bahrain. For dual-language labels and printing needs, Quilon Paper Co. WLL is a reliable option tailored to the local market.
"Our hatch cover packing materials are engineered to ensure water-tightness and weather resistance, essential for protecting cargo holds from water ingress and maintaining cargo integrity under varying sea conditions."
– Qamar Al Jazeera
In addition to basic tools, opt for materials that can withstand Bahrain’s intense heat and humidity.
Weather-resistant Packing Materials
Bahrain’s climate, with summer temperatures often exceeding 40°C, demands specialised materials designed for durability under extreme conditions.
-
Temperature-Control Solutions
Season International Trading & Industries CO. (SITCO) provides industrial-grade packaging specifically designed to protect goods from high temperatures and humidity. -
Moisture Protection Systems
Moisture barrier bags (MBBs) are essential for safeguarding electronics and sensitive items from humidity. They prevent oxidation and block moisture vapour, making them particularly useful during Bahrain’s humid periods. -
Heavy-Duty Storage Options
Pack Kontrol® Weather Resistant Boxes, made with water-resistant adhesive and military-grade corrugated cardboard, are ideal for long-term storage in warehouse conditions.
For inventory that requires extra care, consider these protective materials:
Material Type | Best For | Local Supplier |
---|---|---|
Polyethylene Covers | Standard shipping | SITCO |
Polypropylene Sheets | Warehouse storage | Awal Plastics W.L.L. |
Aluminum Covers | Premium protection | SITCO |
"The company's main focus is temperature stabilization and moisture damage prevention in exports affected by extreme variations in global temperatures."
– Sandra Malouf, President, Eurolog Packing Group
Awal Plastics W.L.L. is another trusted supplier offering protective packaging solutions like air bubble film and PE foam sheets, tailored to handle Bahrain’s unique climate challenges.
Step 3: Setting Up a Weather-Smart Workspace
Creating a workspace that can handle Bahrain's demanding climate requires thoughtful planning. It's not just about safeguarding inventory but also ensuring staff can work comfortably and efficiently. By combining your optimised layout with climate-resistant materials, you can create a workspace that works well for both people and products.
Prioritising Staff Comfort and Safety
The intense heat in Bahrain can lead to fatigue, heat cramps, or even heat exhaustion. To keep your staff comfortable and safe:
- Design ergonomic workstations with adjustable heights to reduce physical strain.
- Use anti-fatigue mats to ease discomfort during long hours of standing.
- Create shaded rest areas so workers can take breaks away from direct heat.
- Equip the workspace with cooling stations, complete with air conditioning, refrigerated water dispensers, and personal protective gear.
Keeping the Temperature in Check
Bahrain’s high temperatures and humidity levels make effective climate control a necessity:
- Install mechanical cooling systems with dehumidifiers. Refrigerant dehumidifiers, for example, are a cost-effective way to manage humidity and prevent overheating or moisture-related damage.
- Regularly service and digitally monitor your cooling and dehumidification systems to catch and fix issues before they escalate.
"With rising electrical costs and problems associated with environmental compatibility of synthetic refrigerants, industrial sectors are finding more reasons to consciously shift away from electrically-driven compression type chillers." - Rajesh Sinha, Business Development Manager with Thermax-USA
Digital sensors that monitor temperature and humidity levels are a smart way to stay ahead of potential problems. They help maintain a workspace that protects both your team and your inventory.
Step 4: Making Packing Fast and Accurate
Streamlining the packing process is key to improving both speed and accuracy. By grouping similar orders together, you can handle 15–20 orders per hour more efficiently.
Group Packing Methods
Smart Batch Processing
- Sort orders based on size and packaging needs.
- Group items requiring the same type of packaging.
- Use standardised materials for common order types.
"You have to ask people to use their brains and their imaginations to solve problems." - Marc Onetto, Amazon
Pair these methods with thorough quality checks to maintain consistency and accuracy.
Dual-Language Quality Checks
Once orders are grouped, verify their accuracy through detailed, bilingual checks. Implementing bilingual systems can ensure at least 96% order accuracy, with top-performing teams achieving up to 99.5%.
Digital Verification Tools
- Bilingual barcode scanning systems.
- Automated weight checks.
- Digital pick lists with real-time inventory updates.
- Integration with warehouse management systems (WMS).
Here’s a structured verification process for better accuracy:
Stage | Primary Check | Secondary Verification |
---|---|---|
Order Entry | Automated data validation | Manual cross-check |
Picking | Barcode scan confirmation | Weight verification |
Packing | Contents verification | Package size validation |
Labelling | Address confirmation | – |
During high-volume periods, smart pick lists powered by data can further reduce errors. These tools guide staff through optimised picking routes and provide step-by-step instructions, making the process efficient for team members, regardless of their language proficiency.
Step 5: Upkeep and Growth Planning
Keeping a packing station running smoothly requires consistent maintenance and forward-thinking growth strategies. Regular upkeep not only helps cut costs but also ensures better accuracy in operations.
Monthly Maintenance Schedule
A well-organized maintenance routine helps prevent minor issues from turning into major setbacks. Here's a monthly checklist to keep everything in check:
Area | Tasks | Frequency |
---|---|---|
Equipment | Inspect barcode scanners, scales, and printers | Weekly |
Storage | Check shelving and reorganize inventory | Bi-weekly |
Workspace | Clean surfaces and ensure ergonomic setup | Daily |
Safety | Test emergency systems and update protocols | Monthly |
Reorganizing fast-moving items regularly and maintaining clear separation between products can significantly reduce errors.
Once a steady performance is secured through routine upkeep, the next step is preparing for peak demand periods.
High-Season Preparation Steps
Routine maintenance is just one part of the equation. Strategic planning becomes crucial when gearing up for high-demand seasons. Ideally, preparations should begin at least six weeks in advance.
Pre-Season Optimisation
Start by using historical data to forecast demand. Hire temporary staff early and provide quick, effective training. Implement real-time analytics to streamline inventory tracking and order management processes.
Adapting to Bahrain’s Climate
Bahrain’s high temperatures can pose challenges, but managing the heat is essential for both inventory safety and staff productivity. Flexible workstation designs can help maintain efficiency during these demanding periods.
"Logistics is something you never think about until it stops working, and we've never come to that point with ShipBob. The services are excellent. Everything just works. We are super happy with ShipBob and very impressed by how well they've pumped out our large volume of orders."
– Sergio Tache, CEO of Dossier
Growth Planning Metrics
To ensure long-term efficiency and success, monitor these key performance indicators regularly:
- Order accuracy rates
- Processing time per package
- Equipment downtime
- Staff productivity levels
- Customer satisfaction scores
Tracking these metrics provides valuable insights into your operation's strengths and areas for improvement, keeping your packing station ready for both everyday demands and future growth.
Conclusion: Building Your Packing Station
Taking the strategies discussed earlier, the next step is to bring them together into a well-organized, forward-looking packing station.
A well-designed packing station is a cornerstone of success in Bahrain's expanding e-commerce market, which is expected to reach BD 468.2 million (US$1.24 billion) by 2025.
Key Elements for an Efficient Packing Station
An effective packing station blends smart planning with practical solutions. Here are some components to consider:
- Automated systems to streamline inventory tracking and update orders efficiently.
- Climate control measures to ensure a consistent and comfortable workspace.
- Ergonomic designs to improve workflow and reduce strain on staff.
- Organized storage to keep inventory accessible and in order.
These elements reflect the core principles shared throughout this guide.
Planning for the Future
With e-commerce user penetration in Bahrain projected to hit 39.8% by 2029, scalability is not just a bonus - it's a necessity. The strategies outlined here, combined with smart layout and equipment choices, will help ensure your operations are ready for growth.
"What you need today, could be entirely different tomorrow. That's why you'll need to design your warehouse operations with the future in mind." – Ruben Jakobs, Executive Sales Director
Maintaining Peak Performance
To keep your packing station running smoothly, focus on these practices:
- Train staff on safety and operational protocols.
- Use real-time inventory management systems for better oversight.
- Implement climate-controlled storage to protect products.
- Conduct regular quality checks to ensure order accuracy.
FAQs
What are the advantages of using a U-shaped packing station layout for small e-commerce businesses in Bahrain?
Why a U-Shaped Packing Station Layout Works for Small E-Commerce Businesses in Bahrain
A U-shaped packing station layout brings practical benefits, especially for small e-commerce operations in Bahrain where space is often at a premium. Here's why it stands out:
- Maximises Space: With its compact design, this layout ensures every square metre is put to good use. Packing essentials like tape, boxes, and labels are all within arm's reach, helping you stay organised even in tight spaces.
- Speeds Up Workflow: By minimising unnecessary movement, this setup streamlines the packing process. Less time spent walking back and forth means quicker order fulfilment and improved productivity.
- Improves Comfort: The layout is designed with ergonomics in mind. Workers can easily access tools without excessive bending or stretching, reducing fatigue and making the job more comfortable.
This arrangement is particularly handy for businesses that deal with products of various sizes. Its flexibility allows for quick adjustments while keeping everything neat and efficient, even in smaller workspaces.
What packing materials and storage solutions work best for Bahrain's heat and humidity?
To shield your belongings from Bahrain's intense heat and humidity, it's essential to use sturdy, weather-resistant materials. Heavy-duty plastic bins with tight-fitting seals are great for keeping moisture at bay. For fragile items, wrap them in UV-protected bubble wrap, and for clothing, vacuum-sealed bags are ideal to limit exposure to humidity. Tossing silica gel packets into boxes can also help by absorbing excess moisture, making them especially useful for electronics and important documents.
When it comes to storage, choosing a climate-controlled environment is key. These spaces maintain temperatures between 12.7°C and 26.6°C, with humidity levels around 55%, offering optimal protection. For added security, use airtight containers or high-density polyethylene bins to keep moisture out. If you need a more adaptable option, PVC storage tents provide a weatherproof barrier against Bahrain's challenging climate.
How can I keep my packing station efficient during busy e-commerce seasons?
To keep your packing station running efficiently during peak e-commerce periods, start by organising it for maximum convenience. Keep essential packing materials - like boxes, tape, and labels - within arm's reach to save time and prevent unnecessary searching. This simple step can make a noticeable difference in speed and help reduce worker fatigue.
Another way to improve efficiency is by streamlining workflows. Tools like barcode scanners or automated systems can help minimise mistakes and increase productivity. Regularly evaluate your processes to spot any slowdowns or inefficiencies, and make adjustments as needed. If you’re facing a surge in demand, think about adding temporary staff or setting up additional packing stations to handle the extra workload smoothly.
Lastly, create a workspace that’s both comfortable and functional. Ensure the area is well-lit and invest in durable, high-quality equipment to maintain performance even during the busiest times. These practical measures will help you stay organised and deliver on customer expectations when it matters most.