How Small Satellite Storage Units Speed Up Delivery
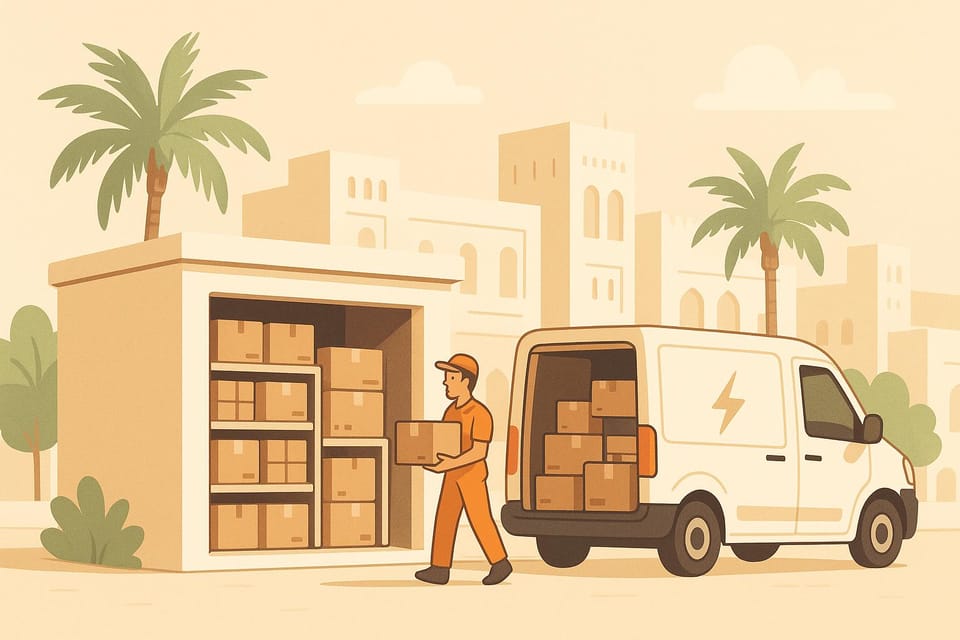
Satellite storage units are transforming last-mile delivery in Bahrain and the GCC by cutting delivery times and costs. These compact hubs bring inventory closer to customers, reducing last-mile delivery expenses, which account for over 50% of total shipping costs.
Key Insights:
- Cost Savings: Last-mile services make up 41% of supply chain costs. Satellite units reduce these by placing inventory near urban areas.
- Faster Deliveries: Urban demand for instant delivery has surged by 30–40%. Satellite depots enable rapid order fulfillment within a 3.2 km radius.
- Climate Control: With the cold chain market expected to reach BHD 7.67 billion by 2026, these units ensure temperature-sensitive goods stay protected in Bahrain's extreme heat.
- Compact Design: Facilities (300–500 m²) use vertical storage and cross-docking to ensure quick inventory turnover, often within hours.
Quick Comparison:
Traditional Warehouses | Satellite Storage Units |
---|---|
Centralised, large facilities | Compact, urban-focused hubs |
Wide aisles, lower turnover | High-density, rapid inventory flow |
Moderate delivery times | Faster, local deliveries |
Satellite storage units are reshaping logistics in Bahrain, aligning with the region's growing e-commerce and urban delivery needs.
What Makes Satellite Storage Units Work
Basic Components and Setup
Satellite storage units, typically ranging from 300 to 500 m², are designed to maximise efficiency by using high-density layouts that eliminate traditional aisles. This setup allows for swift inventory movement and turnover. These units often incorporate push-back racking systems to support both LIFO (Last In, First Out) and FIFO (First In, First Out) inventory methods, along with vertical storage solutions and cross-docking zones. The result? Items flow in and out within just a few hours.
Impact on Delivery Speed
Thanks to their smart design, satellite storage units significantly enhance delivery operations, particularly for local distribution. These compact depots help reduce last-mile delivery costs, which account for more than 50% of shipping expenses, while ensuring quicker, more efficient service. For instance, an urban grocery chain successfully boosted customer satisfaction by leveraging nearby satellite depots for faster deliveries.
"Satellite depots are not just about distribution; they are a testament to our commitment to localized service and ensuring that every customer receives our products at their peak freshness."
- Jane Smith, CEO of FreshSupply Inc.
The table below highlights how satellite storage units outperform traditional warehouses in terms of operational efficiency:
Traditional Warehouses | Satellite Storage Units |
---|---|
Centralised locations for import/export | Strategically placed near customer markets |
Large, sprawling facilities with varied inventory | Compact spaces focused on local distribution |
Designed with wide aisles for navigation | High-density, aisle-free layouts |
Moderate to low inventory turnover | Rapid turnover, often within hours |
With global last-mile deliveries expected to grow by 78% by 2030, the role of satellite storage units is becoming increasingly critical. Their strategic placement close to end-users allows for better accessibility, more precise inventory management, optimised delivery routes, and faster responses to market demands.
"In today's consumer-centric market, satellite depots are not just an advantage; they are a necessity for any F&B business aiming to thrive in the competitive landscape."
Choosing the Right Locations
Where you place your storage units can make or break your delivery efficiency. With last-mile services accounting for a staggering 41% of total supply chain costs, picking the right locations isn't just important - it's essential for keeping operations cost-effective and sustainable.
City Center Storage Points
Urban storage facilities, positioned within an 11–14 km radius of delivery zones, offer speedier deliveries but come with their own set of challenges, particularly around space and costs.
Factor | Impact on Operations |
---|---|
Space Utilisation | Compact layouts with vertical storage to maximise space |
Delivery Windows | Shorter transit times, especially during off-peak hours |
Rental Rates | Higher costs balanced by savings in transportation expenses |
Environmental Impact | Fewer emissions due to shorter delivery routes |
To tackle the space crunch in cities, businesses are repurposing existing structures. For instance, underperforming retail spaces are being transformed into last-mile warehouses, turning what once were liabilities into valuable logistics assets.
"The disruption to the retail sector and the growth of e-commerce will continue to increase the viability and payback of retail-to-industrial property conversions." - CBRE
Storage Hubs Outside Cities
On the outskirts of cities, peripheral hubs provide a different set of advantages, making them a strategic choice for many businesses:
- Lower Costs: Rental rates are significantly cheaper compared to city centres, while still maintaining access to urban areas.
- Room to Expand: These hubs offer more space, allowing businesses to scale operations as demand grows.
- Transport Connectivity: Proximity to major highways and transport networks ensures seamless movement of goods.
However, success hinges on how well these hubs integrate with urban delivery systems. Data shows that profits could drop by as much as 26% over three years if these hubs aren’t optimised. To avoid this, businesses should focus on:
- Defining clear delivery zones based on population density.
- Tracking peak delivery volumes (e.g., grocery operations often handle 250 deliveries per hour).
- Collaborating with local authorities on zoning laws and traffic regulations.
"City logistics requires an understanding of urban geography and supply chain management." - Dr. Jean-Paul Rodrigue & Dr. Laetitia Dablanc
As e-commerce continues to grow, storage hubs outside city centres need to align with shifting demographics and economic trends. They must also maintain easy access to urban delivery zones. This is particularly critical as the last-mile delivery market is projected to hit BD 75.6 billion (USD 200 billion) by 2027.
Setting Up and Running Storage Units
To speed up deliveries, businesses need to combine smart technology with efficient stock management. Properly setting up satellite storage units can significantly improve operations while cutting costs.
Using Tech to Speed Up Work
Modern technology simplifies everything from tracking inventory to ensuring security. Smart systems integrate various components to manage inventory, security, and daily operations effectively:
Technology Component | Primary Function | Operational Benefit |
---|---|---|
Automated WMS | Tracks and manages inventory | Reduces manual errors and improves accuracy |
IoT Sensors | Provides real-time monitoring | Supports predictive maintenance |
Smart Control Systems | Manages lifting and movement | Saves energy and reduces material waste |
HD Camera Systems | Monitors processes and ensures security | Boosts oversight and accountability |
Using sensor systems adds a layer of flexibility and efficiency to storage operations.
"Operational efficiency is at the heart of running a successful self-storage facility. If day-to-day tasks are streamlined, you can focus more on growth and less on administrative burdens."
– Ilyssa Caretsky, Union Realtime
While advanced technology plays a key role, effective stock management is equally crucial for ensuring fast deliveries.
Stock Management Methods
Good stock management ensures that delivery times stay short by keeping inventory organised and accessible. Here are some effective practices:
- Cycle Counting: Regular cycle counts help maintain inventory accuracy without halting operations.
- Set Par Levels: Establish automatic reorder points to keep stock replenished efficiently.
- Standardised Workflows: Create uniform processes for receiving, storing, and dispatching inventory. Use staff ID badges and structured protocols to improve security and reduce errors.
A centralised inventory system allows businesses to oversee stock levels across multiple locations more effectively. This is particularly useful in Bahrain's urban settings, where managing several satellite units is key to keeping delivery operations smooth.
Practice | Implementation | Result |
---|---|---|
ABC Analysis | Focus on high-priority inventory | Makes better use of storage space |
Automated Alerts | Set low-stock triggers | Avoids running out of stock |
Regular Audits | Perform quarterly physical checks | Ensures inventory accuracy |
The success of satellite storage units lies in maintaining accurate inventory control while ensuring that frequently requested items are always easy to access.
Temperature Control for Special Items
Maintaining the right temperature in satellite storage units is crucial for preserving sensitive items and speeding up deliveries. Modern climate control systems make this possible by ensuring optimal conditions.
Setting the Right Temperature
Managing the temperature in climate-controlled storage units is essential to protect inventory. Typically, the recommended temperature range for most items falls between 13°C and 29°C, with humidity levels ideally kept between 30% and 50%.
To achieve this, advanced HVAC systems equipped with AI-driven sensors ensure temperature variations stay within a narrow margin of ±0.5°C. This level of precision is especially critical in Bahrain, where outdoor temperatures can vary significantly throughout the year.
Item Type | Temperature Range |
---|---|
Ambient Storage | 15°C to 25°C |
Cold Storage | 2°C to 8°C |
Frozen Storage | -10°C to -25°C |
Beyond precise climate control, continuous monitoring plays a key role in maintaining product quality. For instance, UNIS highlighted that a major pharmaceutical company managed to cut product spoilage by 30% after adopting precise temperature control in their facilities.
Proper Packing Methods
Good packing practices go hand-in-hand with temperature control, ensuring items stay protected from environmental changes. In Bahrain’s humid conditions, controlling moisture is just as important as temperature for safeguarding inventory.
-
Moisture Protection
Vacuum seals and moisture-absorbing materials are essential. The effectiveness of packaging materials often depends on their Water Vapor Transmission Rate (WVTR). -
Temperature Monitoring
Using real-time temperature monitoring tools, like data loggers, can reduce delivery delays by up to 20%. -
Specialised Containers
Insulated containers with phase change materials (PCM) are ideal for temperature-sensitive items. Vacuum Insulated Panels (VIP) have shown better temperature control compared to traditional foam insulation.
Packing Material | Best Use Case |
---|---|
Aluminised Foam | General Storage |
Polyurethane | Cold Items |
VIP Insulation | Ultra-Sensitive Items |
For additional protection, store items on elevated shelves or pallets. This promotes steady airflow and prevents temperature inconsistencies.
Safety and Upkeep
Ensuring secure and well-maintained satellite storage units is a key factor in delivering goods quickly and reliably.
Security Systems
Modern satellite storage units rely on advanced security systems to ensure safety and efficiency. These systems combine technology and strategy to provide robust protection while also streamlining delivery operations. Here’s a breakdown of key components:
Security Component | Primary Function | Impact on Delivery Speed |
---|---|---|
Smart Access Control | Utilizes PIN codes and license plate recognition | Speeds up entry for authorized users |
Video Analytics | AI-powered surveillance with infrared capability | Ensures round-the-clock monitoring |
Perimeter Detection | Zoned sensors with motion detection | Prevents unauthorized access |
These systems allow for remote monitoring, instant updates to access permissions, and theft prevention through smart electronic locks.
"CPTED encompasses proactive, multifaceted strategies to deter crime by making criminal activity more challenging and increasing the chance of getting caught".
While these advanced security measures are essential, they work best when paired with regular maintenance to keep operations running smoothly.
Regular Maintenance Steps
Routine maintenance not only cuts repair expenses by up to 18% but also prevents disruptions in service. A well-structured maintenance plan should include the following:
- Daily Inspections: Staff should check 5–10 unit doors daily and ensure that critical systems, such as HVAC and security equipment, are functioning properly.
- Seasonal Preparations: HVAC systems should be inspected before peak seasons. In Bahrain's warm climate, major checks during spring and autumn are especially important to avoid breakdowns.
-
Quarterly Reviews: Every three months, assess the following:
- Calibration of security equipment
- Maintenance of door mechanisms
- Efficiency of climate control systems
- Proper functioning of lighting systems
"A little effort now saves significant time and money down the road", says Mike Chorman, Senior Project Director at East Coast Storage Equipment.
"A well-maintained property does more than look attractive to potential customers - it's an important part of ensuring security".
Conclusion
This article has explored how smart positioning, advanced technology, and climate control are shaping a more efficient framework for quicker deliveries. Satellite storage units are reshaping delivery operations across Bahrain and the broader GCC region, significantly cutting last-mile delivery costs, which traditionally accounted for 53% of total shipping expenses.
The success of these satellite storage units comes down to three critical factors:
- Strategic positioning: Compact facilities, ranging from 300–500 m², located in areas like Bahrain Investment Wharf, serve as highly effective distribution hubs.
- Technology integration: RFID systems streamline operations by eliminating over 20 million manual scans daily, boosting efficiency.
- Climate-controlled infrastructure: These units ensure products remain in top condition, even in Bahrain's harsh climate.
"Satellite depots are not just about distribution; they are a testament to our commitment to localized service and ensuring that every customer receives our products at their peak freshness." – Jane Smith, CEO of FreshSupply Inc.
With the global last-mile delivery market expected to reach BHD 109.2 billion by 2031, adopting satellite storage units alongside smarter and more sustainable practices is becoming essential for staying competitive in the GCC's logistics landscape.
FAQs
How do satellite storage units help reduce last-mile delivery costs in Bahrain and the GCC?
Satellite storage units are a game-changer for cutting down last-mile delivery costs in Bahrain and the wider GCC region. These smaller, strategically placed hubs help businesses keep goods closer to areas with high demand, making delivery routes shorter and more efficient. The result? Lower fuel consumption, reduced transportation times, and decreased labour costs, all of which add up to noticeable savings.
On top of that, these units improve inventory management by allowing businesses to respond faster to customer needs without depending solely on large, centralised warehouses. Given Bahrain's hot and humid climate, climate-controlled storage options are especially useful, helping protect goods and maintain their quality. By weaving satellite storage units into their logistics networks, companies can streamline operations and offer quicker, more dependable deliveries to their customers.
What technologies make satellite storage units faster and more efficient for deliveries?
Satellite storage units hinge on several cutting-edge technologies to enhance delivery speed and operational efficiency. Among these are real-time communication systems, automated retrieval mechanisms, and high-speed data processing tools. These components work together to ensure accurate inventory tracking and rapid access to stored items - key factors in seamless last-mile logistics.
Take automated systems, for instance. They maximise storage space and accelerate item retrieval, ensuring operations run smoothly. Meanwhile, advanced communication tools keep businesses informed with live updates on inventory levels and delivery progress. By integrating these technologies, companies can streamline their processes, minimise delays, and better meet customer demands.
How do climate-controlled satellite storage units protect sensitive goods from Bahrain's extreme heat and humidity?
Climate-Controlled Satellite Storage Units
Climate-controlled satellite storage units are purpose-built to shield sensitive items from Bahrain's scorching heat and high humidity. These units keep temperatures steady, usually between 13°C and 29°C, while regulating humidity to prevent moisture-related damage like mould, warping, or corrosion.
By maintaining consistent conditions and ensuring proper airflow, these units safeguard items such as electronics, important documents, furniture, and perishables from wear and tear. On top of that, their sealed design helps keep out dust and other pollutants, offering an added layer of protection for your valuables.