Efficient Micro-warehousing Tips for GCC Entrepreneurs
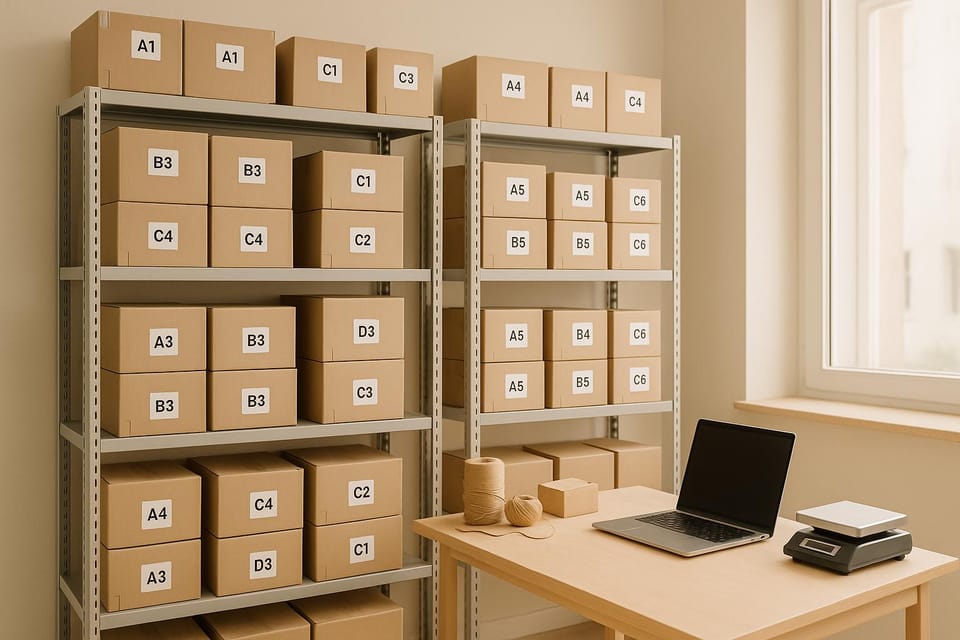
Micro-warehousing is reshaping e-commerce logistics in Bahrain and the GCC. These small urban hubs (279–929 m²) speed up deliveries, cut costs, and improve customer satisfaction. With the GCC's e-commerce market projected to hit BHD 18.85 billion by 2025, here’s why micro-warehousing matters:
- Faster Deliveries: Closer to urban centres for same-day service.
- Cost Savings: Reduced transport and operational costs.
- Automation Benefits: Accurate stock tracking and faster order processing.
- Eco-Friendly: Optimized routes reduce emissions.
Quick Highlights:
- Space Optimization: Vertical storage systems like ASRS save up to 90% floor space.
- Temperature Control: Maintain 18°C–24°C for ambient goods or below -18°C for frozen items.
- Tracking Tools: RFID and barcodes improve inventory accuracy and save time.
- Last-Mile Delivery: Electric vehicles and demand zone mapping enhance efficiency.
For GCC entrepreneurs, adopting these strategies is key to staying competitive in a fast-evolving market.
World’s most efficient warehouse automation solution for order picking and fulfillment | Brightpick
Space Management in Small GCC Warehouses
Smart planning and clever storage solutions can turn small urban warehouses into highly efficient hubs of activity.
Vertical Storage Setup
Using Automated Storage and Retrieval Systems (ASRS) can shrink floor space needs by as much as 90% while keeping everything easily accessible. Similarly, Vertical Lift Modules (VLMs) offer a practical solution, capable of handling up to 140 trays per hour.
Storage Solution | Benefits |
---|---|
ASRS Systems | Cuts floor space usage by up to 90% with automation |
Multi-tier Racking | Makes the most of vertical space for smaller stock items |
Mezzanine Floors | Adds extra workspace without significant costs |
"If we wanted to stay in our current building, our only option was to use the vertical space for additional storage. The Modula system was able to store approximately 90% of our inventory – we couldn't believe it!"
- Aaron Ingram, Product Operations Manager, Innomed
After utilizing vertical solutions, refining aisle configurations can further enhance storage efficiency.
Narrow Aisle Planning
Switching to narrow aisles (about 1.8–2.4 metres wide) can increase pallet positions by 30–40%. However, this shift demands careful planning and specialized equipment. A hybrid aisle setup can strike the right balance between space and functionality:
- Wide aisles (3.6–4.2 metres): Ideal for high-turnover products.
- Narrow aisles (1.8–2.4 metres): Suitable for slower-moving inventory.
- Ultra-narrow aisles (1.7–1.8 metres): Best for bulk storage.
This transition could improve overall storage capacity by 20–25% while ensuring smooth operations. To maintain safety, it’s crucial to focus on proper lighting, clear aisle markings, and thorough operator training for specialized machinery.
Small Item Storage Methods
In addition to aisle adjustments, tailored strategies for small items can make a big difference. Mobile compact shelving systems can boost storage capacity by up to 50% compared to static shelves.
"Modula is a great product, and it has been key in our future growth. We can do much more, much better with much less."
- Chris Lebel, Owner, Industrial Automation Supply
Modern tracking tools like barcodes or RFID technology can cut search times by as much as 60%. To keep things organized, consider:
- Modular bin systems with colour coding for easy identification.
- Adjustable racks that fit various product sizes.
- Mobile shelving units for items that need frequent access.
These strategies are essential for maximizing efficiency in the GCC's compact urban warehouses, where space is at a premium.
Temperature Control for GCC Storage
Managing temperature in Bahrain’s micro-warehouses demands careful planning to protect inventory from the region’s intense heat and humidity. Effective climate control is key to ensuring products remain in good condition.
Heat and Moisture Management
Maintaining stable temperature and humidity levels is critical for preserving inventory quality. The ideal conditions depend on the type of goods being stored:
Storage Type | Temperature Range | Humidity Level | Suitable Products |
---|---|---|---|
Ambient | 18°C to 24°C | 30–50% RH | Electronics, textiles |
Cool | 2°C to 8°C | 50–60% RH | Pharmaceuticals |
Refrigerated | -1°C to 4°C | 85–95% RH | Fresh produce |
Frozen | Below -18°C | 85–95% RH | Frozen goods |
For instance, Kesko’s micro-fulfillment centre in Helsinki implemented separate ambient and chilled systems, achieving an 80% reduction in picking staff and enabling delivery times as short as six hours.
Key strategies to manage heat and humidity include:
- Using HVLS fans to improve air circulation.
- Installing smart thermostats equipped with occupancy sensors.
- Deploying real-time monitoring systems like the UbiBot GS1-AL4G1RS, which track temperatures from -20°C to 60°C and humidity levels between 10% and 90% RH.
These steps form the basis for more advanced measures to limit heat ingress, such as sun protection.
Sun Protection Methods
Cool roofing systems can drastically lower roof temperatures - by as much as 28°C. This is because darker roofing materials reflect only about 20% of sunlight, while lighter-coloured surfaces can reflect up to 80%.
To further reduce indoor heat gains, consider these additional methods:
- Applying UV-filtering window films to minimise heat absorption.
- Installing thermal insulation materials, such as glass wool or spray foam.
- Using moisture barrier bags with foil layers for sensitive goods.
Routine monitoring and upkeep of these systems not only help maintain optimal storage conditions but also contribute to reducing energy consumption over time.
Digital Tools for Stock Management
Efficient space and temperature controls are just one part of the equation for Bahrain's warehouses. Digital tools have become essential for detailed inventory classification and real-time tracking, helping businesses stay on top of their stock.
ABC Stock Classification
ABC analysis is a smart way to prioritize inventory by dividing stock into categories based on its value and importance. This approach is rooted in the Pareto Principle, which suggests that around 20% of inventory items typically account for 80% of the total value.
Category | Value Contribution | Inventory Items | Management Approach |
---|---|---|---|
A Items | 80% | 20% | Daily monitoring, tight control |
B Items | 15% | 30% | Weekly monitoring, moderate control |
C Items | 5% | 50% | Monthly monitoring, simple control |
Steve Copeland, Director at Tempcon, shared an insightful observation: "Using the Netstock classification matrix, we quickly discovered that there were less than a hundred high-value, high-volume items that we should focus on".
While ABC classification helps businesses focus on their most important inventory, automated tracking systems take accuracy and control to the next level.
RFID and Barcode Tracking
RFID technology has revolutionized inventory tracking. A great example is Technowave's project for GANT, which slashed counting time from 10–15 man-hours to just 25 minutes, all while maintaining perfect accuracy.
Software | Starting Price | Key Features |
---|---|---|
Zoho Inventory | BHD 78.4/year | Multi-location tracking, real-time reports |
TallyPrime | BHD 118 (one-time) | Seamless accounting integration |
QuickBooks Online | BHD 11.3/month | Cloud-based accessibility |
Mike Nolan, President of AIS, offers some practical advice:
"RFID is only a tool... Get someone who has experience with RFID implementations in warehouse or industrial settings, describe what you need and let them tell you what is possible and practical".
With precise tracking in place, direct transfer systems can further simplify operations by connecting all stages - from receiving to shipping - into a single, seamless process.
Direct Transfer Systems
Cloud-based Warehouse Management Systems (WMS) are becoming increasingly popular in Bahrain's warehouses. For example, Focus WMS provides customizable workflows tailored to specific business needs, integrating key processes like receiving, put-away, picking, packing, and shipping.
The benefits of these systems include:
- Reduced handling time
- Better order accuracy
- Real-time inventory updates
- Improved coordination across teams
These digital tools, when combined with effective space and temperature management, create a comprehensive strategy for optimizing micro-warehousing in the GCC. For even better results, integrating direct transfer systems with existing ERP platforms can enable smarter, data-driven inventory decisions.
Local Delivery Improvements
Once your storage and inventory systems are running smoothly, the next step is to fine-tune local deliveries. This is especially crucial in Bahrain, where e-commerce is on track to hit BHD 589.5 million by 2027. Efficient final-mile delivery not only boosts operational efficiency but also helps meet the rising expectations of online shoppers.
Green Delivery Options
Sustainability is becoming a key focus in Bahrain, and eco-friendly delivery methods are gaining traction. For instance, electric cargo bikes are proving effective for navigating urban areas like Manama and Seef.
"For last-mile urban transportation, the future is EVs, but the technology is not there yet for heavy goods vehicles. Phasing out fossil fuel road freight vehicles is an essential step to reducing emissions and combatting climate change".
While EVs for smaller deliveries are making headway, the shift for larger freight vehicles still faces technological hurdles.
Delivery Schedule Planning
Carefully planning delivery schedules can make a big difference. Aligning deliveries with local business hours and traffic patterns not only saves time but also cuts down on unnecessary delays.
"Optimized truck journeys through collaboration will lead to a reduced total distance traveled and reduced number of trucks on the road with a consequent reduction in environmental and social costs".
Additionally, demand zone mapping can help refine delivery routes, ensuring that resources are allocated where they’re most needed.
Demand Zone Mapping
Mapping out delivery demand zones is another way to streamline operations. With Bahrain's e-commerce sector growing by 8.30% annually, focusing on high-demand categories like food and personal care can lead to smarter route planning and better warehouse positioning.
"Bahrain offers fertile ground for overseas e-commerce trade and great potential for your business growth. Skip ahead of the competition by delivering a seamless platform experience and shipping strategy".
Safety and Legal Requirements
Running a micro-warehouse in Bahrain requires strict attention to safety and legal standards. Once your space and systems are optimised, ensuring compliance with these regulations becomes crucial for smooth operations.
Security System Setup
Your warehouse's security should be a top priority. Install perimeter fencing with dual-lock entrances, employ round-the-clock security personnel, and set up CCTV surveillance. Additionally, allocate dedicated customs spaces to streamline inspections. All these measures must align with Bahrain's Personal Data Protection Law.
It's also essential to address the safe handling and storage of hazardous materials to safeguard your facility and its surroundings.
Dangerous Goods Safety
Managing hazardous materials comes with its own set of requirements. You’ll need specific permits from Bahrain's Environmental Body to ensure compliance. Below is a quick overview of key safety measures:
Safety Requirement | Implementation Details |
---|---|
Material Analysis | Regularly review and document MSDS (Material Safety Data Sheets). |
Storage Controls | Use temperature-monitored containment areas. |
Waste Management | Implement a system to track hazardous waste. |
Emergency Response | Equip the facility with rapid response protocols and tools. |
"This course provides participants with a comprehensive understanding of hazardous materials, emphasizing safety requirements that are mandated by Bahrain's Civil Defence for their storage and transportation." - ASSP MEC
Additionally, maintain detailed records of hazardous waste disposal, as required by law.
Import-Export Rules
Compliance with customs regulations is another critical aspect of operating a warehouse. To ensure customs adherence, you’ll need a valid land lease contract, a civil defence certificate, an insurance certificate, and an operational diagram. It’s also important to ensure that prohibited goods are not stored or transported, while restricted items must have the necessary approvals. Proper customs declarations are mandatory for all movements.
The Customs Administration of Bahrain clearly states that prohibited goods cannot enter, transit, or leave the country, and restricted goods require approval from relevant authorities. Warehouse operators must maintain accurate documentation for all stored items and allocate sufficient space for customs procedures.
Conclusion: Main Points for GCC Business Owners
Running efficient micro-warehousing operations in the GCC requires a smart blend of technology, space management, and delivery solutions tailored to the region. With e-commerce in the GCC expected to hit BHD 18.85 billion by 2025, businesses must embrace modern urban fulfillment strategies to stay competitive.
Here are some strategies that have shown success in the GCC market:
Strategy | Impact | Implementation Priority |
---|---|---|
Micro-Fulfillment Centers | Speeds up fulfillment by 30–50% | High |
Last-Mile Optimization | Cuts delivery costs by up to 40% | High |
Automated Systems | Lowers per-order costs from BHD 3.780–5.670 to BHD 1.134–2.268 | Medium |
Real-Time Tracking | Improves order visibility and customer satisfaction | Medium |
These methods have already proven their value in the region. For instance, Saudi-based Laverne managed to slash delivery times from four days to just a few hours.
Looking ahead, by 2027, nearly 25% of all e-commerce orders in the GCC will be handled through micro-fulfillment centers. This shift aligns perfectly with Saudi Arabia's Vision 2030 logistics goals and similar initiatives across the region.
To build a strong foundation for these strategies, focus on:
- Choosing strategic locations within spaces ranging from 929 to 4,645 square metres.
- Using automated picking and packing systems.
- Implementing platforms for real-time inventory visibility.
- Leveraging dynamic routing and delivery management tools.
- Applying AI-driven demand forecasting to anticipate customer needs.
Additionally, adopting electric vehicles and optimizing delivery routes can reduce environmental impact while boosting operational efficiency. This approach not only enhances performance but also aligns with broader sustainability goals.
FAQs
What are the best micro-warehousing strategies for GCC entrepreneurs to optimise e-commerce logistics?
GCC entrepreneurs have a great opportunity to fine-tune their e-commerce logistics by using smart micro-warehousing strategies designed to fit the region's specific demands. One key step is to make the most of your storage space with space-efficient shelving systems. This not only keeps your inventory neatly organised but also ensures it's easy to access when needed. Combine this with mobile inventory management apps to monitor stock levels in real time and simplify the order processing workflow.
When it comes to last-mile delivery, integrating technology can make a big difference. Tools like automated systems and real-time tracking not only boost efficiency but also elevate the customer experience. For businesses in Bahrain, climate-controlled storage is especially important to safeguard temperature-sensitive products from the region's intense heat and humidity. By adopting these methods, you can streamline your logistics and set the stage for your e-commerce business to thrive.
How can I effectively manage temperature and humidity in a micro-warehouse in Bahrain’s climate?
To handle Bahrain's hot and humid climate, it's essential to create a controlled environment that safeguards your inventory. Using climate control systems like HVAC units can help maintain consistent temperatures and keep humidity levels between 30% and 50%, which is crucial for preventing mould and protecting your products. Pair this with proper insulation to minimise heat transfer and maintain stable conditions year-round.
In areas prone to excess moisture, dehumidifiers can be a great addition, while ensuring good ventilation will improve air circulation and reduce humidity buildup. Installing environmental monitoring systems can also be a smart move - they track temperature and humidity in real time, enabling immediate adjustments when conditions fluctuate. Don’t forget regular maintenance for all equipment to keep everything running efficiently. These measures can go a long way in shielding your goods from Bahrain's tough climate.
How can small urban warehouses in Bahrain use digital tools like RFID and barcode tracking to improve inventory management?
Digital tools like RFID (Radio Frequency Identification) and barcode tracking are game-changers for inventory management in small urban warehouses. They provide better accuracy, improved efficiency, and clearer visibility into stock levels. With RFID technology, you can scan multiple items at once without needing a direct line of sight. This feature saves time during inventory checks and cuts down on errors - a big advantage in compact warehouse setups where accessing items can sometimes be tricky.
Both RFID and barcode systems automate the process of data collection, keeping inventory records precise and up-to-date. This automation not only trims labour costs but also simplifies operations, making workflows smoother. For small warehouses in Bahrain, adopting these tools means better stock control, fewer discrepancies, and a more efficient way of running daily operations.